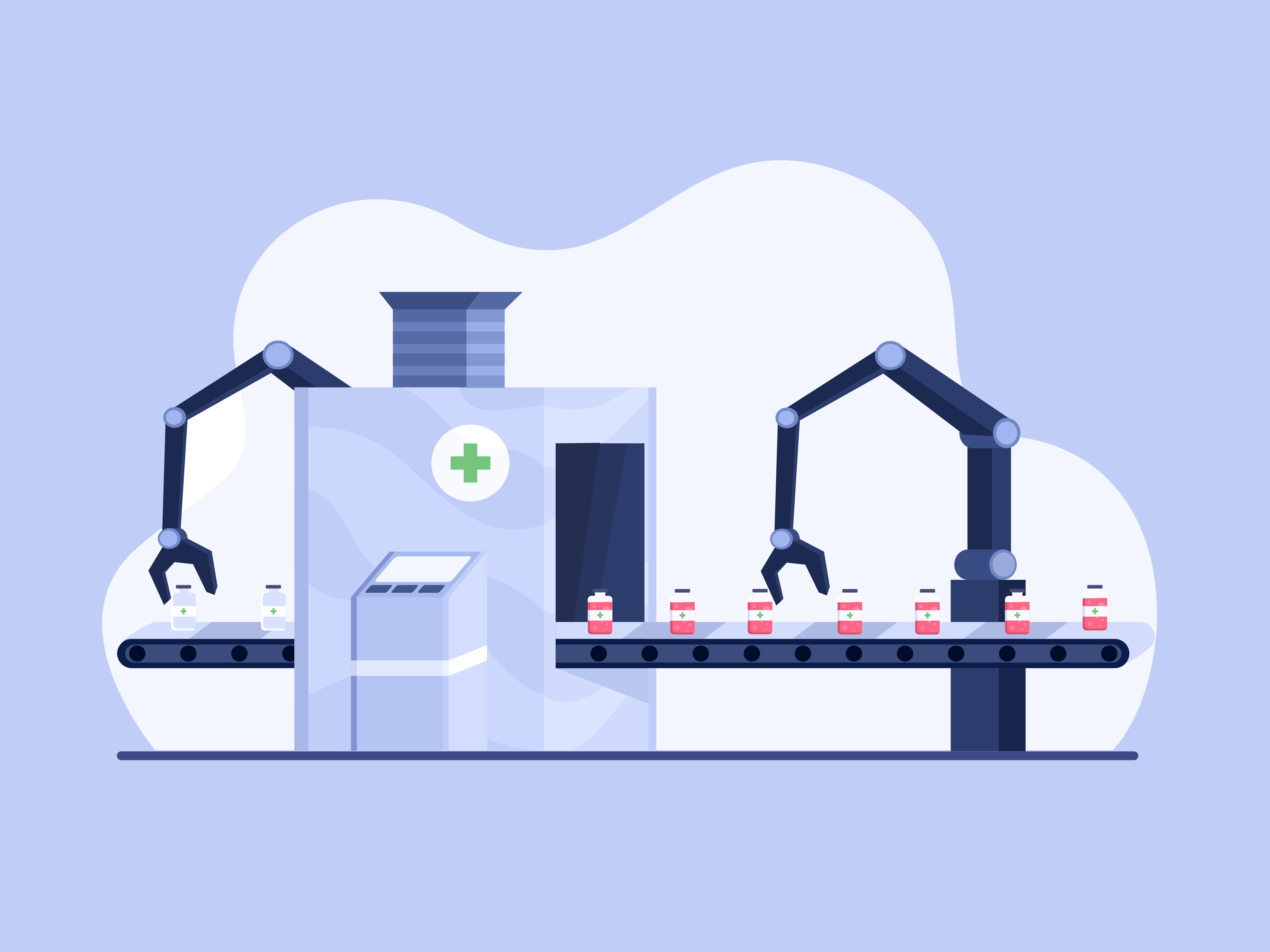
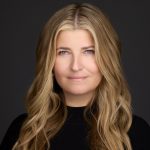
The pharmaceutical industry is one of the most dynamically developing industries. Russian pharmaceutical facilities manufacture drugs to combat a variety of socially significant diseases, emphasizing the urgent need for pharmaceutical production to adapt rapidly to evolving market conditions in order to safeguard the health of citizens. The Pharma-2030 strategy, which has recently been approved by the Government of the Russian Federation, is a clear reflection of the current priorities within the industry. The primary objective of the strategy is to guarantee drug autonomy and national security of the Russian Federation by locally manufacturing the most essential categories of medications, including original drugs, and establishing collaborative partnerships that encompass the entire product life cycle.
The list of vital and essential drugs includes 815 international non-proprietary names. Currently, 82% of them have the opportunity to carry out production stages in Russia. “Pharma-2030” involves expanding the production range of the main active ingredients (pharmaceutical substances and raw ingredients necessary for their production), as well as raw materials, materials, equipment and components to ensure drug safety. Pharmaceutical companies must ensure robust production and supply chains for raw materials and medications to accomplish their goals and top-priority objectives. This entails upholding exceptional quality and efficiency standards.
This course requires a comprehensive examination and improvement of production processes, the modernization of established work patterns, and a concentration on operational effectiveness. Throughout the history of the R-Pharm group of companies, there have been instances where employees have suggested and advocated for improvements in work processes. However, this has not been a widespread or systematic occurrence. Under the current circumstances, there has been a need to make operational efficiency the new philosophy of pharmaceutical manufacturing. To accomplish this task, the group of companies established an operational efficiency department, which began work in 2022.
Since 2022, R-Pharm sites have been embracing the concept of lean production, under the supervision of the department. This implementation involves a continuous process of changes with the goal of identifying and eliminating losses. Losses may be associated with errors in documentation, unnecessary movements of materials, suboptimal organization of workplaces and other factors. The result of eliminating losses is the improvement of the quality of production processes, their duration and costs are reduced. As a result, labor productivity experiences a rise. Managers are not the driving force behind changes, but rather the employees actively involved in production who are fully aware of the strengths and weaknesses of work processes. One of the working groups at the Moscow enterprise of the R-Pharm group of companies proposed the idea of producing disinfectants in-house instead of purchasing ready-made ones for cleaning. This initiative promises significant cost reduction for such products in the future. The goal of the first stage of operational efficiency measures at all R-Pharm sites is to introduce improvements that will save about 450 million rubles per year.
In November 2022, the R-Pharm group of companies took another significant step towards optimizing work processes by participating in the national project “Labor Productivity.” Following an audit conducted by project specialists, two production sites of the flagship R-Pharm plant in Yaroslavl have been chosen to serve as the location for the pilot phase. The implementation of the project program started in March 2023. The diagnostic phase has now been completed. Within three months of work, a team was formed from employees of the production site and the R-Pharm operational efficiency department, which, together with experts, laid the foundation for the further development of the project. In particular, 150 problem areas of work processes were identified, losses associated with excessive transportation were assessed, and internal trainers were certified, whose task will be to train at least 50% of the enterprise’s employees in lean production tools.
The pilot stage, which involves specialists, lasts for six months, and the entire project extends over three years. During this time, the results of the pilot stage should be replicated at all sites of the R-Pharm group of companies.